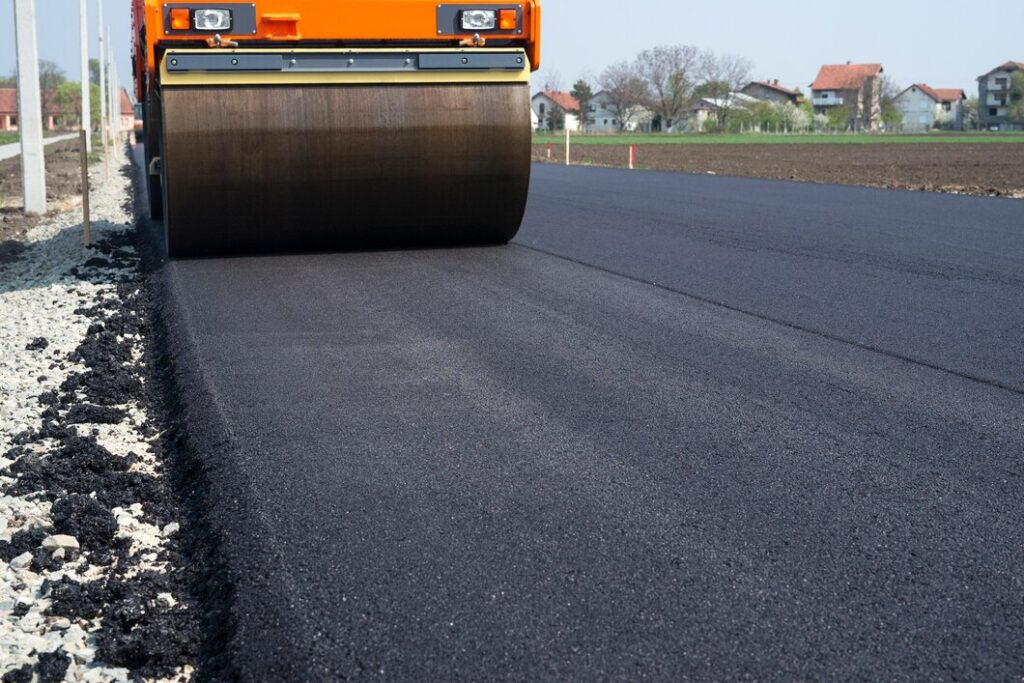
Asphalt paving and sealcoating are essential processes for constructing and maintaining durable, long-lasting driveways, parking lots, roads, and other surfaces. Whether you’re a property owner looking to understand the best way to care for your paved surfaces or a contractor interested in offering the best solutions, this guide will provide you with all the detailed information you need to make informed decisions.
1. Introduction to Asphalt Paving and Sealcoating
Asphalt is one of the most widely used materials for paving roads, parking lots, and driveways due to its durability, cost-effectiveness, and ease of installation. However, like all materials, asphalt can wear over time due to weather conditions, traffic loads, and exposure to various elements. This is where sealcoating comes into play, serving as a protective layer that prolongs the life of asphalt surfaces.
2. What is Asphalt Paving?
Asphalt paving is the process of laying down asphalt mix on a prepared surface to create roads, parking lots, and driveways. It involves a combination of asphalt (a sticky, black, and highly viscous liquid or semi-solid form of petroleum) and aggregates like crushed rock, gravel, or sand.
2.1. Asphalt Paving Process
- Site Preparation: Before the asphalt can be laid, the ground must be properly prepared. This involves clearing debris, grading the surface, and ensuring proper drainage to avoid future issues like flooding.
- Base Layer Installation: A sturdy base is critical to the longevity of the pavement. The base layer, often made of crushed stone or gravel, helps support the asphalt surface and provides drainage.
- Asphalt Application: Once the base is prepared, the hot asphalt mix is laid over it. Paving machines spread the asphalt mix evenly, while rollers compact it to create a smooth, solid surface.
- Finishing and Curing: After paving, the surface must cure and set properly. Curing times vary based on environmental conditions but generally range from 24 to 48 hours for light use.
2.2. Types of Asphalt Mixes
- Hot Mix Asphalt (HMA): The most common type used for large-scale road construction. It is heated and poured at high temperatures.
- Warm Mix Asphalt (WMA): Similar to HMA but mixed at lower temperatures, making it more environmentally friendly and energy-efficient.
- Cold Mix Asphalt: Used for temporary fixes and patches, especially in colder weather where hot asphalt isn’t feasible.
3. Understanding Sealcoating
Sealcoating is the process of applying a protective sealant over asphalt pavements to safeguard them from the damaging effects of water, chemicals, and UV rays. This process not only protects the asphalt but also restores its appearance, making it look new again.
3.1. Purpose of Sealcoating
- Protection from Water Penetration: Water is the leading cause of asphalt degradation. Over time, water can seep into cracks and create potholes. Sealcoating prevents water infiltration.
- UV Protection: The sun’s UV rays can cause asphalt to oxidize, making it brittle and more prone to cracking. Sealcoating acts as a barrier, reflecting UV rays and extending the lifespan of the pavement.
- Chemical Resistance: Oil, gas, and other chemicals from vehicles can deteriorate asphalt surfaces. A sealed surface resists these spills, preventing long-term damage.
- Enhanced Aesthetic Appeal: A freshly sealcoated driveway or parking lot looks dark, smooth, and new. This improves curb appeal and gives a professional appearance.
3.2. Sealcoating Process
- Cleaning the Surface: Before applying sealcoat, the asphalt surface must be clean. Any debris, dirt, and stains are removed to ensure proper adhesion.
- Crack and Pothole Repair: All cracks and potholes should be repaired before sealcoating. This ensures that the surface is even and the sealant provides uniform protection.
- Application of Sealcoat: The sealcoat is applied using a squeegee, brush, or sprayer, depending on the size of the area. Most professionals recommend two coats for optimal protection.
- Curing Time: Just like asphalt paving, sealcoating needs time to cure. It usually takes between 24 to 48 hours for the sealant to dry and harden.
3.3. Types of Sealcoating Materials
- Coal Tar Sealers: Known for their durability and resistance to fuel and oil spills. However, they have a strong odor and can be harmful to the environment.
- Asphalt Emulsion Sealers: More environmentally friendly and less toxic, but may not be as durable as coal tar sealers.
- Acrylic Sealers: A premium option that offers excellent protection and aesthetic benefits but is more expensive than other sealers.
4. Benefits of Asphalt Paving and Sealcoating
4.1. Benefits of Asphalt Paving
- Durability: Asphalt is highly durable and can withstand heavy loads, making it ideal for roadways, parking lots, and driveways.
- Cost-Effective: Compared to other paving materials like concrete, asphalt is more affordable and quicker to install.
- Eco-Friendly Options: Warm mix asphalt reduces the carbon footprint associated with paving by lowering the temperature required during mixing.
4.2. Benefits of Sealcoating
- Increased Longevity: Regular sealcoating can extend the life of asphalt pavements by protecting them from environmental damage.
- Cost Savings: Sealcoating prevents the need for expensive repairs by maintaining the surface before major damage occurs.
- Improved Aesthetics: A sealcoated surface looks newer, more professional, and increases property value.
5. Common Issues and Maintenance Tips
5.1. Common Problems in Asphalt Paving
- Cracking: Over time, asphalt surfaces can crack due to age, weather conditions, or heavy traffic. Regular sealcoating and crack filling can prevent these from worsening.
- Potholes: These are formed when water seeps into cracks, freezes, and expands, causing the asphalt to break apart. Prompt repair is crucial to prevent accidents and further damage.
- Fading and Oxidation: Exposure to the sun and air causes oxidation, leading to a faded appearance and brittle asphalt. Sealcoating helps prevent this by providing a protective layer.
5.2. Maintenance Tips
- Regular Inspection: Routinely inspect asphalt surfaces for any cracks, potholes, or fading. Early detection and repair prevent costly future issues.
- Scheduled Sealcoating: Sealcoating should be done every 2-3 years depending on the traffic and environmental conditions the asphalt is exposed to.
- Proper Drainage: Ensure that the pavement is properly graded to prevent water pooling. Standing water is the enemy of asphalt longevity.
6. Environmental Considerations
Asphalt is often perceived as a pollutant due to its petroleum base, but modern advancements in technology are addressing environmental concerns. From using recycled asphalt to creating eco-friendly sealcoating options, the industry is making strides in sustainability.
6.1. Recycled Asphalt (RAP)
Recycled Asphalt Pavement (RAP) is becoming a popular choice for paving projects. It involves using old asphalt that has been ground up and mixed with new asphalt or used as a base layer, reducing waste and the need for raw materials.
6.2. Sustainable Sealcoating
More contractors are turning to eco-friendly sealcoating materials, such as asphalt emulsion and bio-based products, that offer the same level of protection without harmful environmental impacts.
7. Conclusion
Asphalt paving and sealcoating are vital to creating and maintaining durable, visually appealing surfaces for both residential and commercial properties. Proper installation and regular maintenance, including the timely application of sealcoats, ensure that these surfaces can withstand wear and tear, the elements, and time itself. By understanding the process and benefits of both paving and sealcoating, property owners can make informed decisions that lead to long-lasting, cost-effective solutions for their pavement needs.